SENSORS
SENSORS
The continuous monitoring of the oil condition of the machine on board using sensors is almost inevitable, since the size and thus the distances and routes on the ship continue to increase. A "manual" control is hardly possible in time and practically. It is advisable to install sensors directly in the oil line or in the system in connection with storage and readout units that perform a round-the-clock measurement or record data. Undetected leakage or increased metal abrasion are indicated immediately. Maintenance and repair measures can be carried out promptly, thus saving high repair costs. Due to its modular design, the monitoring system is suitable for all units. Areas of application include the main machine, generators, hydraulic systems,

MT MODULAR MONITORING SYSTEM
Continuous diverse oil analysis
The MT MODULAR MONITORING SYSTEM is a list of various sensor systems that has been developed for continuous real-time monitoring of lubricating and hydraulic oils. The system can be equipped as a complete set of Martechnic ® sensors for a wide range of oil analyzes, or it can be customized for the use of a specific oil system.
FEATURES
-
Measurable parameters
-
Water-in-oil / moisture
-
viscosity
-
Particles
-
iron
ADVANTAGES
-
Continuous diverse oil analysis
-
Plug and play
-
Tailor-made for every application
-
Comprehensive results in real time
-
Extended warning function
-
Improved maintenance practices
The MT MODULAR MONITORING SYSTEM makes it possible to carry out a precise and continuous assessment of the oil system. During the monitoring process, the water content and the degree of saturation of the oil, the contamination by insoluble or metal particles, the contamination by ferromagnetic wear particles as well as the current viscosity value can be measured. By connecting the sensors to the special display unit DATALOGGER, the transmitted data can be saved and evaluated. The deviations of the measured parameters from standard ranges can be recognized using the alarm display.

AHHOI IR + MANIFOLD
The AHHOI - infrared water-in-oil sensor can be equipped with manifold technology for measuring the level of water concentration in up to four different oil systems (e.g. main engine, hydraulic systems and stern tube seals). The infrared measuring process enables the water content to be determined in all three forms: saturated, emulsified and free.
As soon as the sensor is installed and the manifold is connected to the corresponding oil systems using the bypass process, the real-time data on the current water content can be determined directly. The AHHOI sensor measures water in molecular form up to 10000 ppm / 1.0 vol.%. Only a single calibration for the oil types used is required for further continuous monitoring.
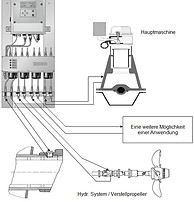
AHHOI IR WATER IN-LINE
IR - water inline sensor, patent no. 2009439
The AHHOI sensor enables continuous inline monitoring of the oil quality through the use of infrared technology and the determination of the level of water concentration in all three forms: saturated, emulsified and free. The main advantage of the water-in-oil sensor is its wide range of applications.
TECHNICAL SPECIFICATIONS
-
Measuring range: 0 - 10000 ppm /
0 - 1.0 vol.% Water -
Operating voltage: 100 - 240 V AC / 50 - 60 Hz, 24 VDC possible on request
-
Pressure primary system: 1 - 10 bar
-
Pressure measuring cell: 0.8 - 1.5 bar
-
Measuring temperature: 0 - 59 ° C
ADVANTAGES
-
Continuous measurement of the water content in oil
-
Detection of water in all three states
-
Low maintenance costs
-
Suitable for new construction and retrofitting
-
Plug and play
Based on the bypass process, the sensor is installed in the engine's lubricating oil system in order to measure the water content in oil in molecular form up to 10000 ppm / 1.0 vol.% In real time. The AHHOI sensor must be pre-calibrated for the type of oil used. The pressure level required for the continuous operation of the sensor is achieved by the integrated valve.

VISCOSITY SENSOR
24/7 viscosity monitoring
The VISCOSITY SENSOR makes it possible to continuously monitor the viscosity, relative permittivity and temperature of lubricating and hydraulic oils in order to create an effective real-time assessment of the oil condition. The constant oil analysis helps to recognize all changes immediately, as well as to determine the quality of the lubricating oil and the engine oil aging.
TECHNICAL FEATURES
-
Measuring range:
-
SAW dynamic viscosity: 8 - 400 mm² / s
-
Rel. Dielectric constant: 1- 7
-
Temperature: -20 ° C to + 85 ° C
-
Accuracy:
-
SAW dynamic viscosity: +/- 5 mm² / s
-
Rel. Dielectric constant: +/- 0.02
-
Temperature: +/- 0.5 K.
-
Power supply: 9 - 33 V
-
Operating pressure: max.50 bar
-
Protection class: IP 67
-
Interface: RS232 / CAN; 4- 20 mA
-
Liquid compatibility: mineral oil, ester liquids, polyalphaolefins
The relevant parameters, namely the SAW dynamic viscosity, the relative permittivity and the temperature are measured and displayed in real time on the special display unit DATALOGGER. After the learning phase of the VISCOSITY SENSOR has ended, the values obtained can also be read at a reference temperature of 40 ° C.

PARTICLE SENSOR
Continuous monitoring of the particle concentration
The PARTICLE SENSOR enables continuous monitoring of hydraulic fluids and lubricating oils to determine insoluble and / or metal particles and the level of their concentration. The sensor technology helps to efficiently follow all changes in the oil condition and enables early detection of wear on machine components.
TECHNICAL FEATURES
-
Measuring range: 4, 6, 14 and 21 µm
-
Purity class according to: ISO 4406: 99 and SAE AS4059
-
Power supply: 9 - 33 V DC
-
Operating pressure: up to 420 bar
-
Flow rate: 50 - 400 ml / min
-
Temperature: -20 to + 85 ° C
-
Protection class: IP 67
-
Interface: RS-232 / CAN; 4 - 20mA
-
Data storage: 3000 data records
-
Liquid compatibility: mineral oil (e.g. HLP), ester liquids (e.g. HEES / HETG)
The PARTICLE SENSOR uses the so-called light extinction principle with laser technology for the optical counting of the covered particles and their classification in a measuring cell with regard to their size and number. The measured values are displayed in accordance with ISO 4406: 99 and SAE AS 4059. With its high operating pressure of up to 420 bar, the sensor can be installed directly in the pressure line. The data received is recorded, transferred to the DATALOGGER and saved over a longer period of time.

STANDARD MOISTURE SENSOR
Continuous water-in-oil monitoring
The STANDARD MOISTURE SENSOR detects free or dissolved water in oil by continuously measuring the relative humidity. The real-time monitoring of the degree of saturation of oil with water allows all changes that occur to be recognized directly in order to enable effective operation of the engine system.
TECHNICAL FEATURES
-
Measuring range: 0 - 100% (rel.humidity)
-
Temperature: -20 - + 85 ° C
-
Power supply: 9 - 33 VDC
-
Operating pressure: max. 10 bar
-
Protection class: IP 67
The STANDARD HUMIDITY SENSOR constantly measures the humidity value that is processed on the DATALOGGER display unit. The degree of saturation (in%) is calculated in the range from 0% (no water detected) to 100% (complete saturation / existence of free water). The sensor is particularly relevant with regard to unsaturated ester oils. Since portable test devices measure the level of water concentration with the help of reagents, this measurement method is not suitable for ester oils.

MOISTURE SENSOR PLUS
Continuous determination of the water content in oil
The HUMIDITY SENSOR PLUS is an improved version of the HUMIDITY SENSOR STANDARD, which enables real-time monitoring of three oil parameters (relative humidity, relative permittivity and the conductivity of the oil). Because of the proposed possibility to measure, record, save and automatically evaluate the data, the sensor can be described as a semi-intelligent device of a new generation.
TECHNICAL FEATURES
-
Measuring range:
-
Relative humidity: 0 - 100%
-
Relative permittivity (dielectric constant): 1-7
-
Conductivity: 100 - 800000 pS / m
-
Temperature: -20 - + 85 ° C
-
Supply voltage: 9 - 33 VDC
-
Operating pressure: max. 50 bar
-
Protection class: IP 67
-
Interface: RS 232 / CAN; 4- 20 mA
-
Liquid compatibility: mineral oil, ester liquids, polyalphaolefins
The screw-in sensor helps to continuously assess all occurring changes in the degree of saturation of the oil with water together with the relative dielectric constant and the conductivity at the current temperature. The values obtained are transferred to the special display unit DATALOGGER. After completing the learning phase and creating the required database, the measured values are also available at a reference temperature of 40 ° C. Using the data compiled, it is possible to calculate the remaining life of the oil and to determine optimal maintenance and oil change intervals.

FE SENSOR
Continuous monitoring of the ferromagnetic particles
Through continuous monitoring, the FE-SENSOR enables the determination of the ferromagnetic wear particles and, accordingly, an exact assessment of the condition of lubricating and hydraulic oils. Since the degree of concentration of the ferromagnetic particles demonstrates possible ongoing friction processes in the machine components and wear in oil systems, the use of sensor technology allows constant monitoring of all changes that occur in order to take suitable corrective measures.
TECHNICAL FEATURES
-
Measuring range: 0-100%
-
Accuracy: +/- 1%
-
Supply voltage: 9 - 33 VDC
-
Operating pressure: max. 10 bar
-
Temperature: -40 ° C to + 85 ° C
The inductive measuring principle is used to measure the number of ferromagnetic wear particles. The particles are collected on the head of the FE-SENSOR, which is equipped with a permanent magnet. The output signal in the range from 0 to 100% is related to the amount of particles distributed on the sensor surface. Fine particles (micrometer range) and coarse ferromagnetic fragments (millimeter range) can be distinguished. The data is continuously transferred to the special unit DATALOGGER and stored in order to ensure an effective assessment.

Data storage device
The DATALOGGER is part of the MT MODULAR MONITORING SYSTEM, which is suitable for the recording, storage and display of the data received. Although the device has been specially developed for its own sensor system, the DATALOGGER can also be programmed and individually adapted to the special properties of a specific application.
TECHNICAL FEATURES
-
Ambient conditions for storage:
-
Temperature .: 0-60 ° C
-
Moisture: 0-95%
-
Ambient conditions operation:
-
Temperature: 5-50 ° C
-
Moisture: 0-95%
-
Internal data storage: 1000 records
-
LED display
-
Power supply: 9-33 VDC
-
Interface: RS-232, analog 4-20 mA
-
SD card up to 4 GB
The DATALOGGER receives and continuously processes the measured oil parameters, displays them and saves them. For this purpose, the device is equipped with the internal memory and the external SD card. Thanks to the integrated transmission mode and the software from Martechnic ® , the information received can be displayed on a computer for evaluation. The DATALOGGER enables effective data tracking in the process of remote monitoring of the oil condition.
